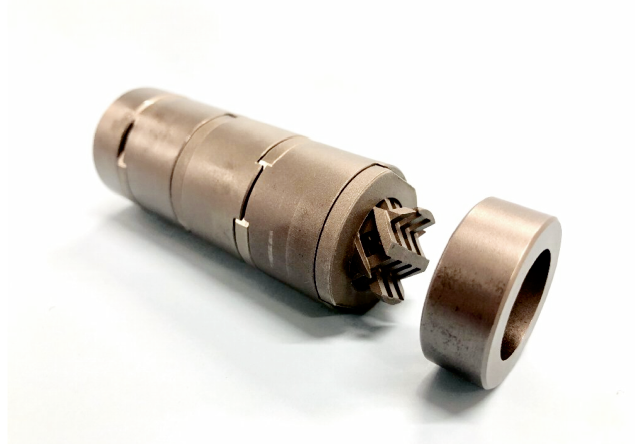
プロミックスミキシングエレメント SMK-R17/4(通常はミキシングノズルに内蔵される)
1:はじめに
射出成形機においては、発明当初から現代に至るまでオープンノズルを用いるのが一般的である。溶かした樹脂を金型に射出し、冷却され固化した段階で金型から抜型し、製品として出荷される。本来であれば単に金型内に樹脂を射出できれば良いので、ノズルは単に機械と金型のインターフェースに過ぎない。
しかしながら、過去と比較し現代では多種多様な樹脂や添加剤が開発され、経済性や品質特性などにおいて極限まで難易度が高まりつつある。コスト低減、品質改善の観点に立てば、マスターバッチや添加剤等の削減、サイクルタイム短縮による稼働率、キャビバランスによる不良率の低減などが必須となっている。加えてさらなる効率の向上が求められ、従来の技術だけでは対応しきれない状況となってきたのは否めない。これらを実現するためには、樹脂の流れを積極的にコントロールし、温度・速度・分散においていかに均質化を図るかが非常に重要な「鍵」となる。
2:樹脂の流動形態の改善 (温度・速度)
単純な空管を溶融樹脂が流れる場合、図1のようにせん断速度が山なりとなり、図2のように温度分布がW型になることが知られている。金型が単独ゲートの場合は大きな問題とならない場合が多いが、キャビ数やゲート数が多い場合はこれらが不良の原因となることが多い。その対策としてミキシングノズルを採用し、速度と温度の均質化を図り、キャビ毎、ゲート毎の樹脂の温度、速度を一様にすることが可能である。
結果、ノズルとシリンダー温度を下ることができ、射出圧力も下げられ、固化時間が短くなるのでサイクルタイムも短縮することが可能となる。但し、射出工程において若干ながら圧力損失が発生するので、薄肉、高速射出には不向きな場合があるため、事前に充分な検討を行う必要がある。
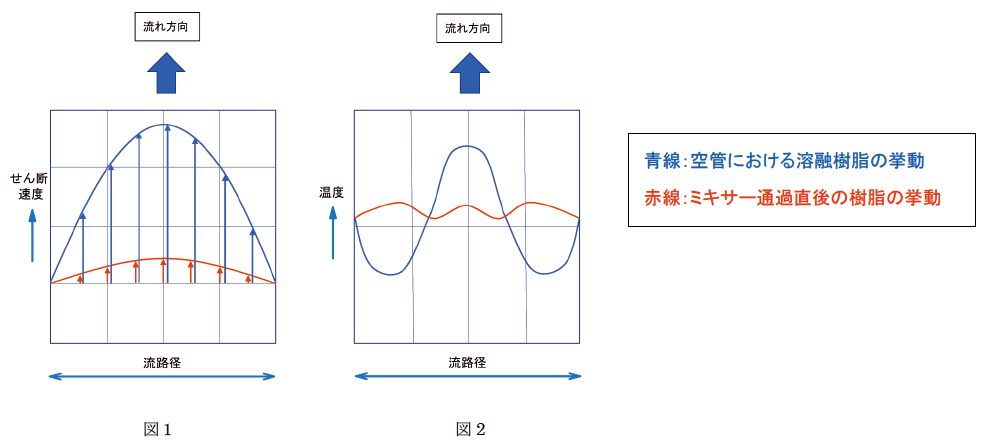
3:樹脂の混錬性の改善 (分散)
マスターバッチによる顔料、染料、添加剤においては、高い分散性が求められる。日本で一般的になってきたサブフライトやダルメスクリューは、そもそも大変高い混錬性を有しているものの、近年、その要求はさらに厳しくなってきたと言えよう。そのためスクリューのみでは混錬性が足らず、多少なりとも分散性に問題が出てくるのは否めない。また、単純な空管の場合、前項同様、高粘度流体ではせん断速度があるため、内壁面のスキン層と中心部の流動樹脂とは分散性が異なっていることも理解できる。特にベース樹脂と分離しやすい添加物や発泡剤が入っている場合はより顕著となる。
それを改善するため、ミキシングノズルを使うことは大変意義がある。ミキシングエレメントは圧力損失が発生するので、射出工程の妨げにならない様充分に注意する必要があるが、サブフライトやダルメスクリューと組み合わせることでエレメント数を削減できるため、一番良いバランスを探ることが出来る。写真1はプロミックスミキシングノズルでの混錬具合を示した写真である。
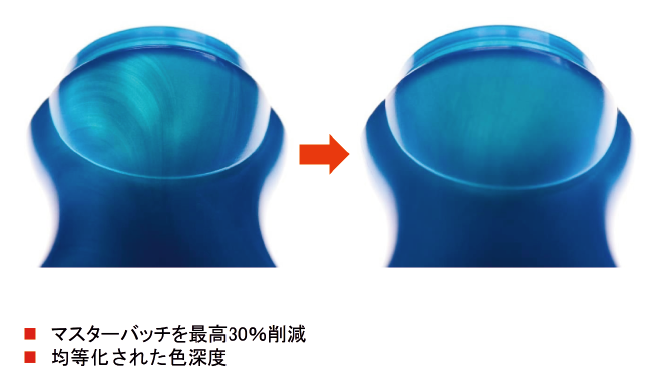
4:プロミックスミキシングノズルのメリット
これまでの記述で、一般的なミキシングノズルを使用することのメリットを述べてきた。いろいろなミキシングノズルがこれまで開発されてきているが、プロミックスミキシングノズルは、その中でも特に高粘性流体に最適なミキサーであると言える。写真2及び3は、赤白2色のエポキシ樹脂を流し、その混錬具合を撮影した。
この分野においては、途中に絞りを入れ流速を上げてミキシング性能を上げる手法、流体自身の回転速度を上げて分散性を上げる手法など、その手段は多岐に渡る。しかしながらが、プロミックスは高粘性流体に特化し独創的な設計思想を有し、溶融樹脂材料のミキシングに最適と言える。
ミキサーの始まりから終わりまで開口断面積が変化しないシンプルな構造となっており、加えて内部構造は、円筒の容器に入れた溶融樹脂を、左右に配した二本の熊手を交互に交差させ撹拌するような構造になっている。そのため、混錬後の溶融樹脂は層状にならず、高いミキシング性能を期待することが出来る。結果、分散性が良くなるので、計量時間を短くすることも可能となる。これらのことから、プロミックスは、高い次元で圧力損失と混錬性をバランスさせているミキシングノズルであると言える。
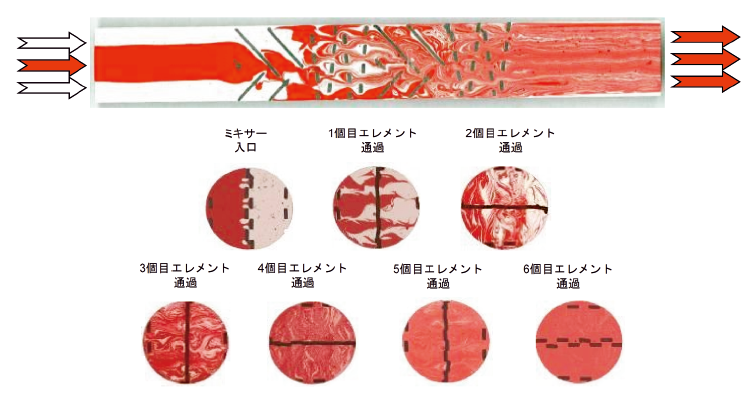
併せて、プロミックスミキシングノズルは、チップ、ボディ、アダプター及びエレメントで構成されており、容易に分解清掃が可能となっている。具体的な作業としては、オーブン等で樹脂を取り除き、チップ及びアダプターを外し、プレス等を用いてボディよりエレメントを押し抜いた後、エレメントのクリーニングを行うことで完了する。通常のミキシングノズルは分解清掃が難しい場合が多い。
が、本品は、そもそもメンテナンスを前提にした設計のため、完璧な分解清掃が可能となり、安定的な操業が長期にわたり可能となる。
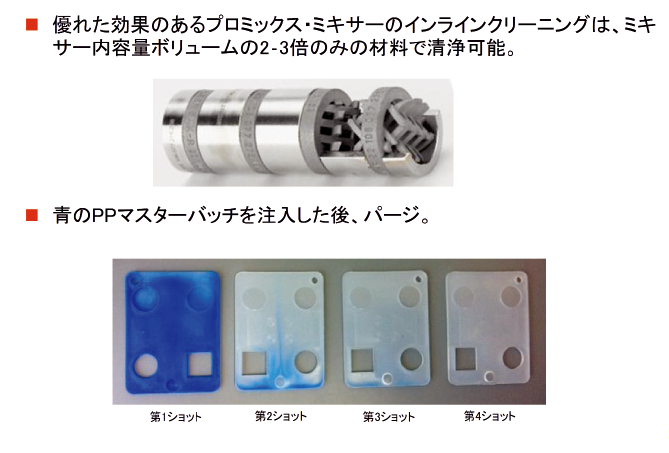
シンプルな構造は色替え時にも有効に働く。写真5及び6に示すように、概ねミキサー内のボリュームの2倍から3倍の材料(樹脂によっては5倍程度)で色替えを完了することが可能である。
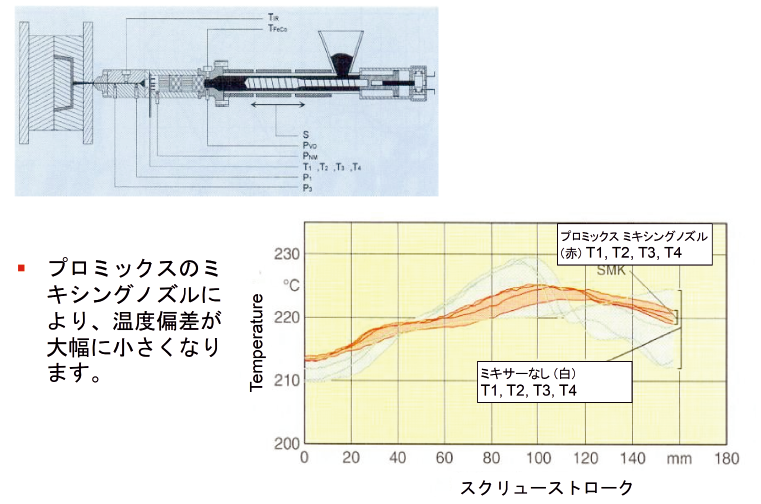
図3はスクリューのストローク上の温度変化をとらえたグラフである。ミキサー無しの場合、流路内の温度分布は図2青線のようになるとともに、スクリューストローク上の温度変化は図3の白となる。が、ミキシングノズルを搭載すると、流路内温度分布は図2の赤線のようになり、スクリューストローク上の温度変化も図3の赤となる。このことから、射出全域にわたりトータルに温度変化を制御できることが理解できる。またトータル的に樹脂温度が低くなるため、型開が早くすることが可能となる。分散が良くなることで計量時間も短くなるので、どちらにせよサイクルタイムの短縮に繋がるのは間違いない。結果として、速度、温度、分散の全てにおいて、安定的に均質化を行うことが可能になったと言える。
プロミックスミキシングノズルのメリット
1:カラーストリークの低減
2:ミキシング性能に比較し、低い圧力損失
3:均質化された色深度(外観の向上) (カラー材、可塑剤、化学発泡剤、各種添加物)
4:マスターバッチを最高30%削減 (カラー材、可塑剤、化学発泡剤、各種添加物)
5:温度プロファイル均質化による白点の防止
6:寸法精度の向上
7:再生樹脂の利用率改善(破砕樹脂及び再生樹脂の使用量増加)
8:ホットランナー使用時のキャビティーバランス及びゲートバランスの向上
9:容易な分解清掃作業
10:早期の型開閉及び短い計量時間による、サイクルタイムの短縮、
11:低背圧での計量
12:ノズル、シリンダー温度の低減
13:樹脂の物性値の低減防止
5:発展的応用例
プロミックスミキシングノズルは、エレメントのみでも供給可能している。ホットランナーにおいて、エレメントを流路に設置することにより、より発展的な使い方が考えられる。
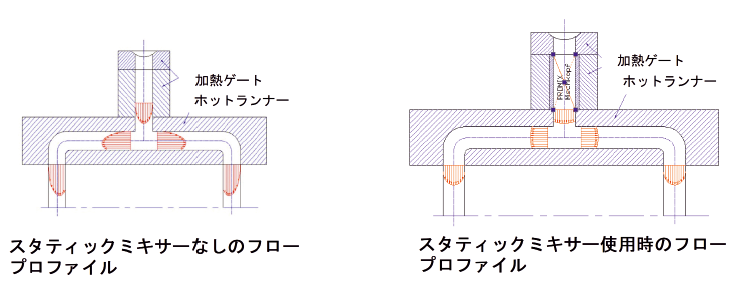
スプルーブッシュ直下に配置することにより、分岐直前で温度、せん断速度、分散性を全てニュートラルにすることにより、キャビティ―毎の均質性を保つことが可能となる。
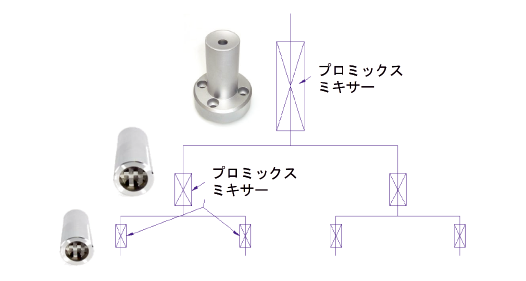
PET樹脂によるプリフォーム成形のように強度を要求される場合、より強固な構造であるミックスゲートを推奨する。
圧損の累積により成形性を損なう場合はあるものの、各段階全てにエレメントを挿入することも可能である。樹脂の粘度が低く、インジェクションレートが低い場合において、極めて高い樹脂の均質性を求める場合、一考する価値があると言える。
6:終わりに
ミキシングノズルは依然より認識されてきたが、射出時の圧損やメンテ等いくつかの理由により、そのメリットが享受できず採用を見送られるケースが散見された。しかしながら、プロミックスミキシングノズルは、その独創的な構造により、圧力損失と均質性を極めて高いレベルでバランスさせることが出来、SMKにおいては、そのメンテナンス性も非常に高いことから、適用範囲が大きく広がったと考える。(SMKやミックスゲートなど、一体構造の製品は弊社メンテサービスにてクリーニングが可能)加えてエレメントのみの販売も行わられるため、金型内部への搭載と言うこれまでにないアプリケーションも可能となった。
ミキシングノズルの数々のメリット、そして新しい金型へのミキシングエレメントの搭載は、混錬の新しい概念をお客様に提供し、その期待に充分応えることが出来ると考える。よって、今後の射出成形機に求められる厳しい要求に対し、しっかりと対応できるユニットであると言えよう。
また、此処にあげた数々のメリットは、高い生産性及び成型技術の高度化に繋がり、ひいては環境負荷を大きく低減することができると考えられる。これにより、新たな「環境に優しい成型技術」としての適用も今後拡大していくと期待される。
以上
20200226